Hazard identification
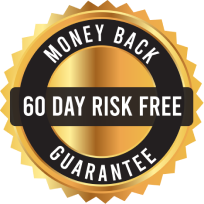
Hazard identification
How to identify hazards in a workplace?
There are many potential hazards that can be present in any workplace. Some of the most common workplace hazards include slips, trips and falls; exposure to harmful substances; and ergonomic issues.
Slips, trips and falls are one of the most common types of workplace accidents. They can occur due to spills, cluttered work areas, poor lighting, or simply because of the nature of the work being done. Slips, trips and falls can lead to serious injuries, including broken bones, concussions, and even death.
Hazard identification is an important part of any safety program. By identifying hazards in the workplace, employees and employers can take steps to control or eliminate them. There are a number of ways to identify hazards, including conducting a hazard assessment, observing work practices and reviewing incident reports.
Conducting a hazard assessment is one of the most effective ways to identify hazards in the workplace. A hazard assessment is a systematic examination of the workplace to identify potential hazards. It should be conducted by a qualified person who is familiar with the particular workplace and the types of hazards that may be present.
About this course
- Training Provider: OHS.com.au with AlertForce (RTO Code 91826)
- Location: Online
- Course length: Approx. 4 hours
- Time: Self-paced
- Certification / Accreditation: Certificate of Completion*
- CPD Points: Yes. 4 points as certificate of completion
Background – When should hazard identification be done?
Hazard identification can be done in a number of ways, depending on the circumstances. Sometimes it can be done during the design and implementation phase of a project, such as when designing a new process or procedure. Other times, it can be done before tasks are undertaken, such as when checking equipment or following processes. Reviewing surroundings before each shift can also help to identify potential hazards.
While tasks are being done, it is important to be aware of changes, abnormal conditions, or sudden emissions. This can help to identify potential hazards before they cause an incident. Inspections, both formal and informal, can also be a useful tool for hazard identification. Supervisors and health and safety committees can also help to identify potential hazards.
To ensure all hazards are found the follow steps should be taken:
- Look at all aspects of the work and include non-routine activities such as maintenance, repair, or cleaning.
- Look at the physical work environment, equipment, materials, products, etc. that are used.
- Include how the tasks are done.
- Look at injury and incident records.
- Talk to the workers: they know their job and its hazards best.
- Include all shifts, and people who work off site either at home, on other job sites, drivers, teleworkers, with clients, etc.
- Look at the way the work is organized or done (include experience of people doing the work, systems being used, etc).
- Look at foreseeable unusual conditions (for example: possible impact on hazard control procedures that may be unavailable in an emergency situation, power outage, etc.).
- Determine whether a product, machine or equipment can be intentionally or unintentionally changed (e.g., a safety guard that could be removed).
- Review all of the phases of the lifecycle.
- Examine risks to visitors or the public.
Course outline
Alertforce’s Hazard Identification training course is of the utmost importance in any industry. To best ensure a safe working environment for all, it is necessary to regularly conduct Hazard Identification and Risk Assessment (HIRA) as well as Hazard Prevention and Control (HPC) procedures. HIRA allows for the identification of potential workplace hazards, while HPC implements controls to mitigate the risks associated with those hazards.
The objectives of Alertforce’s training course is to bring about greater awareness of workplace hazards and the ways in which they can be controlled. By understanding the Recognition, Evaluation and Control of Hazards (REACH) process, its requirements and benefits, employees will be better equipped to identify and mitigate risks in their workplace.
This course is designed to create safer workplaces.
Learning form
All Hazard Indentification course participants are encouraged to watch the videos and engage in group discussions after each video is finished. Facilitators and participants can review the key points from each video and module using the provided support material.
There are many ways to view and participate in discussions.
- E-learning Format
- Face-to face safety meetings
- Forum
Participants can upload the training videos to e-learning and view them online. Participants can review the support material online and answer any questions.
Face-to-face safety meetings allow participants to watch videos and participate in discussions. Face-to-face meetings allow for greater interaction and engagement, but can be logistically challenging.
You can also upload the videos to a forum. Participants can access the videos and other support materials via a private forum, company website, or by uploading them to a forum. Each module contains the answers to your questions.
You can also complete the course via email. Participants can email their answers to the discussion questions once they have watched the videos.
No matter how the material is delivered, all participants should have access to it. The support material includes discussion questions as well as the video script. Participants can use the questions to explore the effects of safety practices on their organization.
The modules also include scripts and reference materials. These materials allow participants to review and research the key points of the lesson.
Facilitators and participants can use the video scripts and questions to help them create an action plan. Participants can take specific steps and make suggestions to use the plan in their work environment.
SKU:
Course Highlights:
- On-demand Training
- Complete on Any Device
- Quality Focused
- Fast Certification
- Tax Deductable
- 100% Online
- 24 Months Unlimited Course Access
- Self-print Certificate
Couldn't load pickup availability
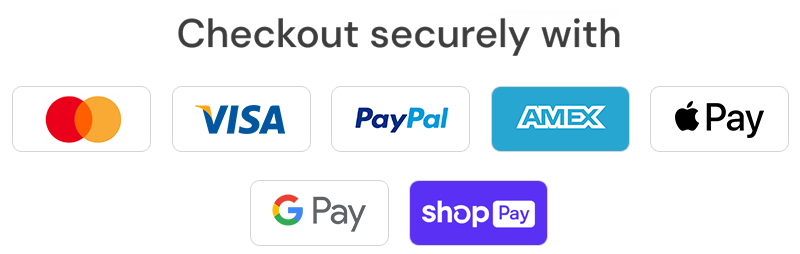
"Very detailed information, with the ability to shuffle and skip past parts that I knew. I actually enjoyed doing it. I was refreshed after completing the course. All in all, a fantastic refresher course."
Luke W."Straight forward and easy to understand. Thanks, OHS this is my second Refresher course."
Anonymous"Quick & relatively easy, done from the comfort of home."
David B"Really great courses on OHS website, would use this site again."
RhysADDITIONAL EXTRA BONUSES with OHS.com.au
Claim up to $1271.95 worth of Extra Bonuses
with every purchase
- Your personal copy of Safety Legends E-Book (value $39.95)
- $100 off your first case from Naked Wines (value $100)
- Upto 350,000 Bonus AMEX Frequent Flyer points* (value $1000)
- Complimentary Access to two online courses** (value $132)
$1271.95 EXTRA VALUE - JUST FOR YOU INSIDE!
* New customers when you successfully sign up for a new personal / business credit card ** Indigenous Cultural Awareness / Impacts of Climate Change coursesDescription
How to identify hazards in a workplace?
There are many potential hazards that can be present in any workplace. Some of the most common workplace hazards include slips, trips and falls; exposure to harmful substances; and ergonomic issues.
Slips, trips and falls are one of the most common types of workplace accidents. They can occur due to spills, cluttered work areas, poor lighting, or simply because of the nature of the work being done. Slips, trips and falls can lead to serious injuries, including broken bones, concussions, and even death.
Hazard identification is an important part of any safety program. By identifying hazards in the workplace, employees and employers can take steps to control or eliminate them. There are a number of ways to identify hazards, including conducting a hazard assessment, observing work practices and reviewing incident reports.
Conducting a hazard assessment is one of the most effective ways to identify hazards in the workplace. A hazard assessment is a systematic examination of the workplace to identify potential hazards. It should be conducted by a qualified person who is familiar with the particular workplace and the types of hazards that may be present.
About this course
- Training Provider: OHS.com.au with AlertForce (RTO Code 91826)
- Location: Online
- Course length: Approx. 4 hours
- Time: Self-paced
- Certification / Accreditation: Certificate of Completion*
- CPD Points: Yes. 4 points as certificate of completion
Background – When should hazard identification be done?
Hazard identification can be done in a number of ways, depending on the circumstances. Sometimes it can be done during the design and implementation phase of a project, such as when designing a new process or procedure. Other times, it can be done before tasks are undertaken, such as when checking equipment or following processes. Reviewing surroundings before each shift can also help to identify potential hazards.
While tasks are being done, it is important to be aware of changes, abnormal conditions, or sudden emissions. This can help to identify potential hazards before they cause an incident. Inspections, both formal and informal, can also be a useful tool for hazard identification. Supervisors and health and safety committees can also help to identify potential hazards.
To ensure all hazards are found the follow steps should be taken:
- Look at all aspects of the work and include non-routine activities such as maintenance, repair, or cleaning.
- Look at the physical work environment, equipment, materials, products, etc. that are used.
- Include how the tasks are done.
- Look at injury and incident records.
- Talk to the workers: they know their job and its hazards best.
- Include all shifts, and people who work off site either at home, on other job sites, drivers, teleworkers, with clients, etc.
- Look at the way the work is organized or done (include experience of people doing the work, systems being used, etc).
- Look at foreseeable unusual conditions (for example: possible impact on hazard control procedures that may be unavailable in an emergency situation, power outage, etc.).
- Determine whether a product, machine or equipment can be intentionally or unintentionally changed (e.g., a safety guard that could be removed).
- Review all of the phases of the lifecycle.
- Examine risks to visitors or the public.
Course outline
Alertforce’s Hazard Identification training course is of the utmost importance in any industry. To best ensure a safe working environment for all, it is necessary to regularly conduct Hazard Identification and Risk Assessment (HIRA) as well as Hazard Prevention and Control (HPC) procedures. HIRA allows for the identification of potential workplace hazards, while HPC implements controls to mitigate the risks associated with those hazards.
The objectives of Alertforce’s training course is to bring about greater awareness of workplace hazards and the ways in which they can be controlled. By understanding the Recognition, Evaluation and Control of Hazards (REACH) process, its requirements and benefits, employees will be better equipped to identify and mitigate risks in their workplace.
This course is designed to create safer workplaces.
Learning form
All Hazard Indentification course participants are encouraged to watch the videos and engage in group discussions after each video is finished. Facilitators and participants can review the key points from each video and module using the provided support material.
There are many ways to view and participate in discussions.
- E-learning Format
- Face-to face safety meetings
- Forum
Participants can upload the training videos to e-learning and view them online. Participants can review the support material online and answer any questions.
Face-to-face safety meetings allow participants to watch videos and participate in discussions. Face-to-face meetings allow for greater interaction and engagement, but can be logistically challenging.
You can also upload the videos to a forum. Participants can access the videos and other support materials via a private forum, company website, or by uploading them to a forum. Each module contains the answers to your questions.
You can also complete the course via email. Participants can email their answers to the discussion questions once they have watched the videos.
No matter how the material is delivered, all participants should have access to it. The support material includes discussion questions as well as the video script. Participants can use the questions to explore the effects of safety practices on their organization.
The modules also include scripts and reference materials. These materials allow participants to review and research the key points of the lesson.
Facilitators and participants can use the video scripts and questions to help them create an action plan. Participants can take specific steps and make suggestions to use the plan in their work environment.

- Money Back Guarantee
- Save Time & Money
- Tax Deductible
- 1000's Trained Each Month
- Quality-Focused
- Peer Reviewed Courses
- Trusted Industry Partner
- Fast Certification
- 60 Day Guarantee
- *See refund policy
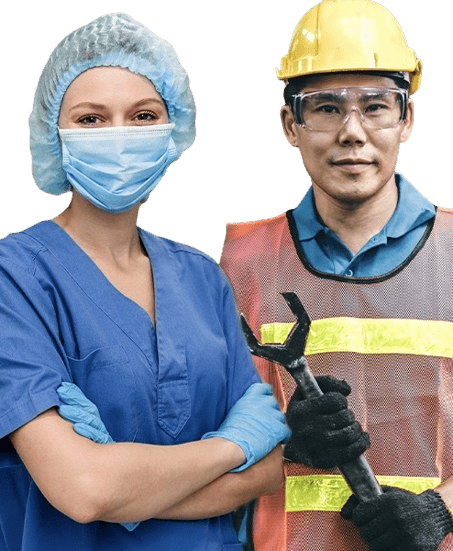

Got multiple people needing to do a course? We will get back to you within a day!
Student Reviews

Couldn't load pickup availability
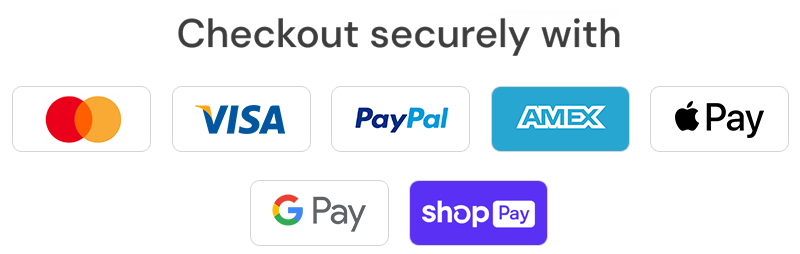
Contact Us!
Contact form
ADDITIONAL EXTRA BONUSES with OHS.com.au
Claim up to $1271.95 worth of Extra Bonuses
with every purchase
- Your personal copy of Safety Legends E-Book (value $39.95)
- $100 off your first case from Naked Wines (value $100)
- Upto 350,000 Bonus AMEX Frequent Flyer points* (value $1000)
- Complimentary Access to two online courses** (value $132)
$1271.95 EXTRA VALUE - JUST FOR YOU INSIDE!
* New customers when you successfully sign up for a new personal / business credit card ** Indigenous Cultural Awareness / Impacts of Climate Change coursesDescription
How to identify hazards in a workplace?
There are many potential hazards that can be present in any workplace. Some of the most common workplace hazards include slips, trips and falls; exposure to harmful substances; and ergonomic issues.
Slips, trips and falls are one of the most common types of workplace accidents. They can occur due to spills, cluttered work areas, poor lighting, or simply because of the nature of the work being done. Slips, trips and falls can lead to serious injuries, including broken bones, concussions, and even death.
Hazard identification is an important part of any safety program. By identifying hazards in the workplace, employees and employers can take steps to control or eliminate them. There are a number of ways to identify hazards, including conducting a hazard assessment, observing work practices and reviewing incident reports.
Conducting a hazard assessment is one of the most effective ways to identify hazards in the workplace. A hazard assessment is a systematic examination of the workplace to identify potential hazards. It should be conducted by a qualified person who is familiar with the particular workplace and the types of hazards that may be present.
About this course
- Training Provider: OHS.com.au with AlertForce (RTO Code 91826)
- Location: Online
- Course length: Approx. 4 hours
- Time: Self-paced
- Certification / Accreditation: Certificate of Completion*
- CPD Points: Yes. 4 points as certificate of completion
Background – When should hazard identification be done?
Hazard identification can be done in a number of ways, depending on the circumstances. Sometimes it can be done during the design and implementation phase of a project, such as when designing a new process or procedure. Other times, it can be done before tasks are undertaken, such as when checking equipment or following processes. Reviewing surroundings before each shift can also help to identify potential hazards.
While tasks are being done, it is important to be aware of changes, abnormal conditions, or sudden emissions. This can help to identify potential hazards before they cause an incident. Inspections, both formal and informal, can also be a useful tool for hazard identification. Supervisors and health and safety committees can also help to identify potential hazards.
To ensure all hazards are found the follow steps should be taken:
- Look at all aspects of the work and include non-routine activities such as maintenance, repair, or cleaning.
- Look at the physical work environment, equipment, materials, products, etc. that are used.
- Include how the tasks are done.
- Look at injury and incident records.
- Talk to the workers: they know their job and its hazards best.
- Include all shifts, and people who work off site either at home, on other job sites, drivers, teleworkers, with clients, etc.
- Look at the way the work is organized or done (include experience of people doing the work, systems being used, etc).
- Look at foreseeable unusual conditions (for example: possible impact on hazard control procedures that may be unavailable in an emergency situation, power outage, etc.).
- Determine whether a product, machine or equipment can be intentionally or unintentionally changed (e.g., a safety guard that could be removed).
- Review all of the phases of the lifecycle.
- Examine risks to visitors or the public.
Course outline
Alertforce’s Hazard Identification training course is of the utmost importance in any industry. To best ensure a safe working environment for all, it is necessary to regularly conduct Hazard Identification and Risk Assessment (HIRA) as well as Hazard Prevention and Control (HPC) procedures. HIRA allows for the identification of potential workplace hazards, while HPC implements controls to mitigate the risks associated with those hazards.
The objectives of Alertforce’s training course is to bring about greater awareness of workplace hazards and the ways in which they can be controlled. By understanding the Recognition, Evaluation and Control of Hazards (REACH) process, its requirements and benefits, employees will be better equipped to identify and mitigate risks in their workplace.
This course is designed to create safer workplaces.
Learning form
All Hazard Indentification course participants are encouraged to watch the videos and engage in group discussions after each video is finished. Facilitators and participants can review the key points from each video and module using the provided support material.
There are many ways to view and participate in discussions.
- E-learning Format
- Face-to face safety meetings
- Forum
Participants can upload the training videos to e-learning and view them online. Participants can review the support material online and answer any questions.
Face-to-face safety meetings allow participants to watch videos and participate in discussions. Face-to-face meetings allow for greater interaction and engagement, but can be logistically challenging.
You can also upload the videos to a forum. Participants can access the videos and other support materials via a private forum, company website, or by uploading them to a forum. Each module contains the answers to your questions.
You can also complete the course via email. Participants can email their answers to the discussion questions once they have watched the videos.
No matter how the material is delivered, all participants should have access to it. The support material includes discussion questions as well as the video script. Participants can use the questions to explore the effects of safety practices on their organization.
The modules also include scripts and reference materials. These materials allow participants to review and research the key points of the lesson.
Facilitators and participants can use the video scripts and questions to help them create an action plan. Participants can take specific steps and make suggestions to use the plan in their work environment.

- Money Back Guarantee
- Save Time & Money
- Tax Deductible
- 1000's Trained Each Month
- Quality-Focused
- Peer Reviewed Courses
- Trusted Industry Partner
- Fast Certification
- 60 Day Guarantee
- *See refund policy
Student Reviews

Course Highlights:
- On-demand Training
- Complete on Any Device
- Quality Focused
- Fast Certification
- Tax Deductable
- 100% Online
- 24 Months Unlimited Course Access
- Self-print Certificate
Couldn't load pickup availability
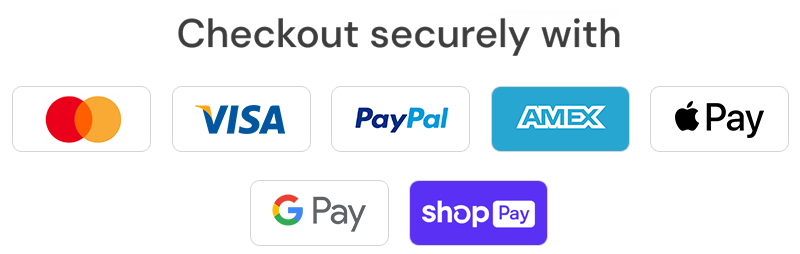
"Very detailed information, with the ability to shuffle and skip past parts that I knew. I actually enjoyed doing it. I was refreshed after completing the course. All in all, a fantastic refresher course."
Luke W."Straight forward and easy to understand. Thanks, OHS this is my second Refresher course."
Anonymous"Quick & relatively easy, done from the comfort of home."
David B"Really great courses on OHS website, would use this site again."
Rhys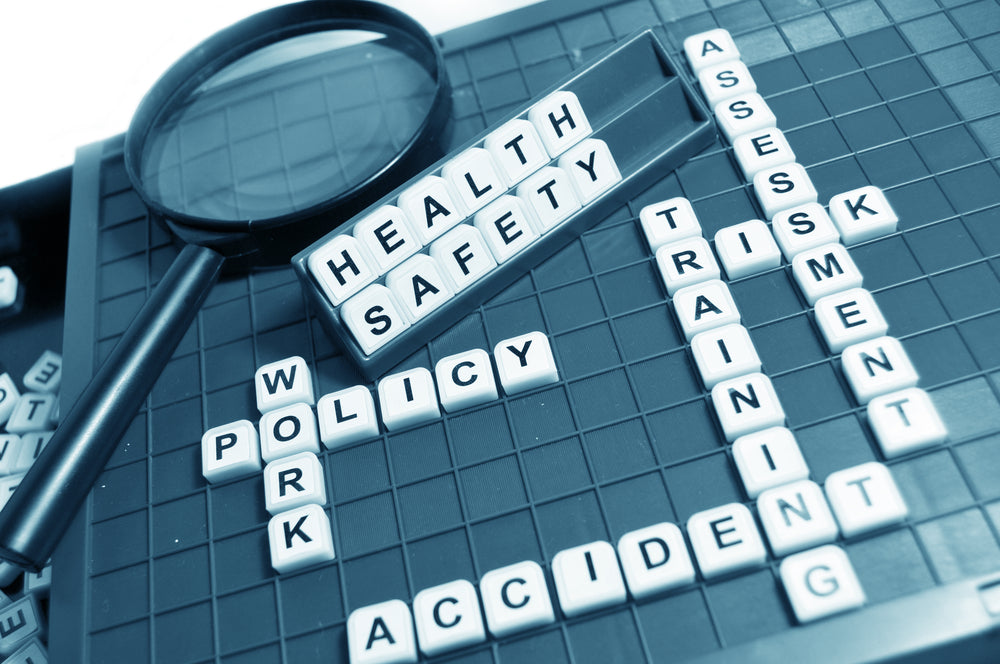
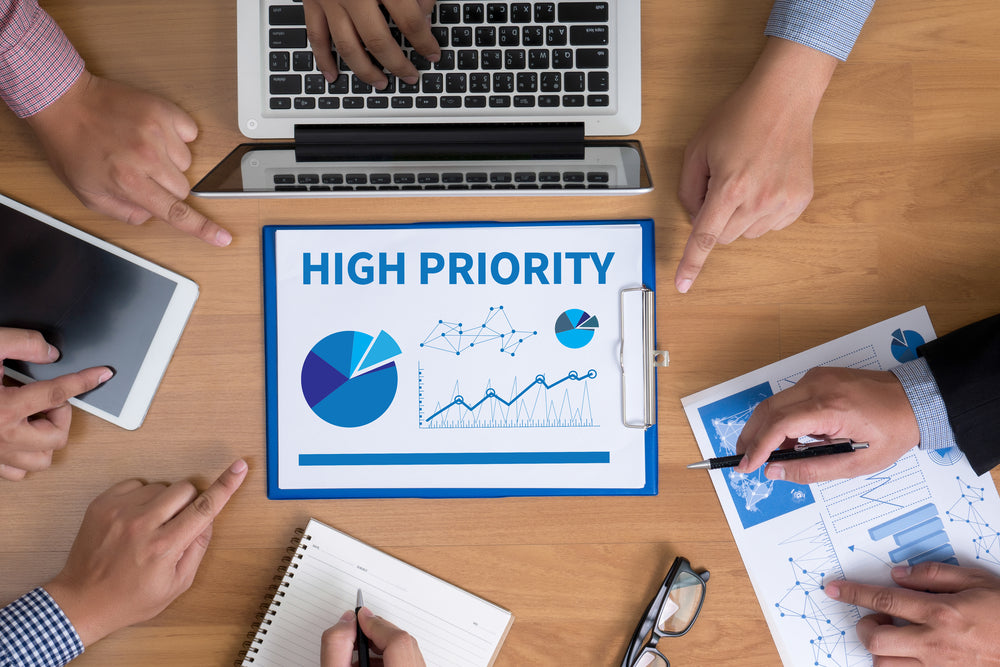
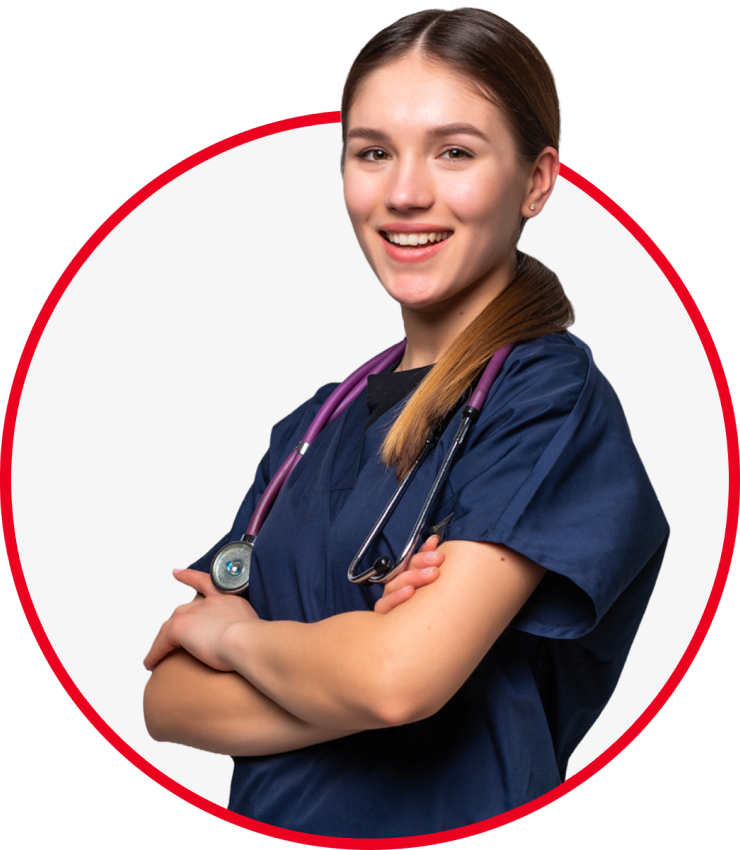
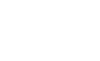
Are you from a large organisation? Contact us for a group quote!

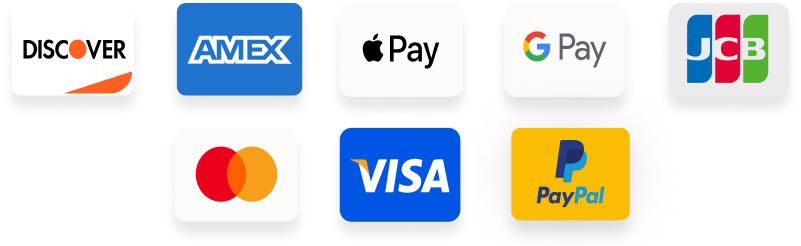
OHS offers practical and effective online health and safety training courses, having been in the training industry since 1999. Our mission is to deliver online refreshers that align seamlessly with our clients' busy lives, ensuring they remain up-to-date with the latest industry standards.
At OHS, our training programs, including NDIS Training, Safety Training, Staff Training and VOCs/High Risk Refreshers, are designed to be both flexible and cost-effective, allowing everyone to take advantage of professional development opportunities. You won't have to keep searching for terms like 'First Aid Training Online Certification', 'First Aid Training Tenders' or 'Hr Training For Hr Professionals Sydney'; we've streamlined access to essential knowledge.
OHS allows you to match your training to your lifestyle, giving you a choice between individual courses or an annual subscription with unlimited access. Instead of scrolling through results for search terms like 'manual handling training canberra', 'quality management training' or 'management training courses', contact us to learn more or buy a course today.